
La longueur du document peut en première impression faire peur mais après lecture des textes publiés et rédaction de ce dernier et étant moi même l'un des principaux inconscients non masqués, je peux vous dire que je suis pas prêt de le lâcher mon masque ! Je conseille donc très fortement à tous shapers amateurs de prendre le temps nécessaire à sa lecture. Nous avons essayé "d'aérer" au mieux le texte pour le rendre plus digeste...


Les données sont extraites de différentes études faites pour le compte de l’ «Association Clean Shaper*» et reproduite avec leur autorisation.
LES PAINS

1.Le pain de mousse polyuréthane
1.1. Introduction
Le pain de mousse polyuréthane a été utilisé dans la fabrication des planches de surf depuis les années 1950 dès l’avènement des matériaux composites dans l’industrie aéronautique. En effet l’utilisation de polyuréthane avec de la résine polyester offre un compromis légèreté / souplesse / résistance à ce jour inégalé.

Le problème de la mousse polyuréthane est qu’elle a un impact non négligeable sur la santé des ouvriers qui la fabriquent et sur l’environnement. Les constituants de la mousse polyuréthane (les isocyanates) sont en effet des composés chimiques toxiques très volatiles qui se dispersent donc rapidement dans l’atmosphère. Ces composants sont très délicats à
manipuler et le brûlage de la mousse polyuréthane provoque l’apparition de fumées toxiques et même mortelles à certaines concentrations. En outre le polyuréthane est à ce jour non recyclable d’un point de vue technico économique.
Depuis une vingtaine d’années la fabrication des pains de mousses pour la fabrication des planches de surf était dominée par une entreprise américaine (Clark foam) qui avait développé une gamme de pains « pré shapés » qui permettait de diminuer le travail du shaper mais également limitait les chutes d’usinage. Cette entreprise utilisait du toluène pour la
fabrication de la mousse ce qui est devenu interdit aux Etats-Unis. Pour cette raison et d’autres raisons sûrement économiques, l’entreprise a fermé ses portes.

Depuis, de nombreuses usines se sont lancées de par le monde dans ce marché devenu ouvert. Cela s’est fait au détriment souvent de la qualité des produits (process difficile à maîtriser) mais également au dépend de la santé des travailleurs de ces usines et de l’environnement en général.
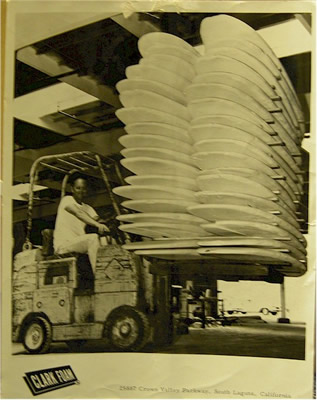
1.2. Le polyuréthane
La majorité des planches de surf dans le monde sont fabriquées à partir d’un pain de mousse polyuréthane drapé de tissu de verre qu’on imbibe de résine polyester. Il s’agit de la technique de fabrication la plus utilisée par les artisans et il n’existe pour l’instant pas de machine pouvant remplacer la stratification manuelle.
Pain de mousse polyuréthane + tissu de verre + résine polyester

1.3. Les constituants de la mousse polyuréthane
Les mousses polyuréthanes résultent principalement de l’addition de polyisocyanates sur des polyols. Les différents constituants sont mélangés vigoureusement puis coulés dans des modules de moulage.
Polyisocyanates (TDI ou MDI) + Polyols + Catalyseur + Tensio actifs + Agents d’expansion = Mousse polyuréthane
1.4. Les risques toxicologiques et environnementaux des principaux constituants de la mousse polyuréthane.
a. Les isocyanates
Au cours de la fabrication et de leur mise en oeuvre, les isocyanates entraînent des risques importants :
- le TDI (2,4 ou 2,6 diisocyanate de toluylène) est classé Très Toxique et est particulièrement dangereux à cause de sa grande volatilité.
- le MDI (diisocyanate de diphénylméthane) est classé Nocif par inhalation et est moins volatile
Il est donc important de garder en tête que même le MDI n’est pas un produit écologique, il s’agit d’un constituant moins toxique que le TDI mais qui présente quand même une certaine toxicité.
Totalement polymérisés (c'est-à-dire après la stratification), les produits finis sont physiologiquement inactifs. Toutefois ils peuvent renfermer des restes de catalyseurs et ainsi dégager des vapeurs d’isocyanates pendant quelques heures voire quelques jours.

Selon le fabricant de pains de mousse on peut retrouver des concentrations plus ou moins importantes de vapeurs d’isocyanates dans les pains de mousse. Elles résultent en général d’une mauvaise maîtrise du process de catalyse. Ces poches de vapeurs sont dégagées lors de l’usinage du pain (l’étape du shape) et vont donc intoxiquer directement le shaper qui ne porte pas de masque adapté aux vapeurs. En effet lors de l’étape du shape un masque à poussières est le plus souvent utilisé et suffit normalement à protéger les voies respiratoires des poussières mais pas des vapeurs organiques si les pains de mousse sont mal catalysés.

Ces vapeurs d’isocyanates sont peu à peu neutralisées dans l’environnement par la vapeur d’eau atmosphérique mais participent donc à l’augmentation de la pollution photochimique à basse altitude.
b. Les polyols
Les polyols ajoutés aux isocyanates sont des produits relativement inoffensifs lorsqu’ils sont purs. Ils sont souvent livrés avec des catalyseurs qui peuvent par contre entraîner une légère toxicité.
1.5. Les projets de pains de mousse polyuréthane « alternatifs »
Plusieurs sociétés se sont lancées dans la fabrication de mousse polyuréthane sans TDI (sans toluène) et ont communiqué sur le fait de produire un pain de mousse écologique. Elles utilisent pour la plupart du MDI à la place mais comme nous l’avons vu la toxicité de ce constituant est quand même importante. Il est probable que la réglementation européenne exigera dans les années qui viennent l’arrêt de l’utilisation du toluène pour la fabrication d’un certain nombre d’objets. Il s’agit donc d’une anticipation de la réglementation.
2. LE POLYSTYRENE

2.1. Introduction.
Le polystyrène est utilisé comme pain de mousse dans la fabrication des planches de surf depuis une vingtaine d’année. Il faut utiliser de la résine époxy dans ce cas car la résine polyester est incompatible chimiquement avec le polystyrène.

Le marché du polystyrène évolue à la hausse depuis quelques années sous l’impulsion d’une marque américaine (Surftech) communicant sur une solidité accrue et des performances plus élevées que le process de fabrication classique (il n’existe pas à notre connaissance d’étude scientifique prouvant ces déclarations).

2.2. La fabrication de la mousse polystyrène
Le polystyrène résulte de la polymérisation du styrène sous l’action de catalyseurs.
On ajoute un agent d’expansion pour obtenir (selon la technique) du polystyrène expansé ou extrudé.
Styrène + Catalyseur + Agent d’expansion (pentane) = Polystyrène (expansé ou extrudé)

2.3. Les risques toxicologiques et environnementaux du polystyrène
Le risque principal vient de l’utilisation du styrène comme solvant lors de la fabrication de la mousse (et parfois du toluène !). Le styrène a en effet une action toxique sur le système nerveux central.
A la différence de la mousse polyuréthane le polystyrène peut être recyclé. Il est d’ailleurs recyclé au Japon depuis le début des années 1980. Un réseau de collecte et de valorisation existe en France (http://www.ecopse.fr). Encore faut-il avoir une usine de recyclage dans les environs…

3. Comparaison des deux types de fabrication des planches utilisés dans l’artisanat
Le problème essentiel de la mousse polyuréthane provient de l’utilisation du toluène qui doit être absolument éliminé du process de fabrication ce que certaines entreprises sont en passe de réussir complètement. L’incinération pose également des problèmes de traitement des fumées car du cyanure d’hydrogène est produit lors de la combustion du polyuréthane.
Le polystyrène n’est pas une mousse écologique, elle contient des solvants comme le styrène qui reste un produit pétrolier polluant. Son intérêt principal est d’être techniquement recyclable. Le bilan environnemental peut être affiné par une analyse du cycle de vie (A.C.V) des deux types de mousse mais la technologie évolue très rapidement et une analyse précise (et coûteuse) serait très vite obsolète.

Le principal avantage de la mousse polystyrène est d’être techniquement et économiquement recyclable. Mais dans beaucoup de pays et d’îles où l’on pratique le surf il n’y a souvent pas d’usine de recyclage du polystyrène. Les chutes de polystyrène et les planches cassées suivent et suivront encore pendant plusieurs années le chemin classique des ordures ménagères (dépôts sauvages à l’air libre, enfouissement ou incinération) en provoquant des pollutions
visuelles.
Il faut noter que même avec un pain de mousse recyclable, les planches en fin de vie seront difficilement recyclables car une délamination sera nécessaire pour enlever le tissu de verre imbibé de résine. Ces coûts de pré traitement vont sérieusement handicaper une filière de recyclage des vielles planches.

3. Conclusions
Il n’existe donc pas à ce jour (et malgré certaines auto déclarations) de pain de mousse écologique. Des progrès sont en cours en utilisant des produits issus de ressources renouvelables ou en éliminant l’utilisation de composants toxiques mais il reste toujours des composés d’origine pétrolière. La fin de vie des planches pose également un problème dans la
mesure où il n’est pas économiquement intéressant de passer du temps à rassembler les planches, les collecter, les trier, les délaminer et les envoyer dans un centre de recyclage.

La directive européenne Reach va avoir comme conséquence de limiter la fabrication et l’utilisation d’une certaine partie des produits chimiques classés comme très dangereux pour la santé et l’environnement. Les industriels de la fabrication de produits chimiques vont devoir innover et développer de nouveaux produits plus respectueux de l’environnement. Il
s’agit d’un tournant majeur pour la plupart des artisans qui devront faire face à une évolution des produits chimiques et donc des process de fabrication.

Les résines

1. Rappel : Technique de La stratification
La stratification peut être réalisée avec des résines polyester ou époxyde. En cas de stratification polyester, la mousse polystyrène ne pourra servir de noyau.
Les principales caractéristiques des résines utilisées sont : leur transparence, leur faible viscosité, un temps de gel relativement court (quelques minutes), une grande tenue aux UV et leur aptitude au ponçage.
Les résines sont renforcées de tissus de verre relativement fins (de 125 ou 250 g / m²). Le renfort est généralement plus important sur le pont que sur la carène.
La stratification consiste à venir mouiller les tissus et à enlever l’excédent de résine à l’aide d’une raclette comme le montre les photographies page suivante.
La stratification est réalisée face après face, chacune d’entre elle nécessitant environ 600 g de résine (pertes comprises).
Une fois la stratification terminée, un glaçage est réalisé afin d’avoir une surface la plus lisse possible. Ce glaçage correspond à une nouvelle couche de résine à laquelle on ajoute de la paraffine qui viendra créer en séchant une fine pellicule de surface. Cela permet de faciliter le ponçage qui rend l'état de surface parfaitement lisse.
2. Les résines
2.1. Les résines polyesters :
Les résines polyesters (ou UP) sont issues d’une réaction de polycondensation entre un polyol et un polyacide. Il s’agit de la réaction d’estérification. Ces résines se présentent sous forme de solution dans un monomère. Elles se rigidifient sous l’effet d’un catalyseur + accélérateur ou catalyseur + chaleur.
Il s’agit de la résine la plus utilisée dans les composites. Les réactifs jouent un rôle primordial sur les propriétés des résines et influencent également la structure chimique des résines polyesters. On distingue quatre familles de polyesters : ](orthophtaliques, isophtaliques, chlorée et bisphénol).
Les plus utilisées sont les résines orthophtaliques et isophtaliques :
- Les résines orthophtaliques sont moins coûteuses et moins performantes que les autres familles de résines. Elles sont les plus courantes et sont le résultat d'une polycondensation entre l'anhydride phtalique (ou anhydride maléique) et le propylène glycol.
- Les résines isophtaliques sont de meilleure qualité que les résines orthophtaliques et présentent une plus grande résistance à l'humidité. Elles sont obtenues par addition d'un acide isophtalique et d'un alcool. Elles sont couramment utilisées dans le secteur du nautisme (coques de bateau, planches à voile) ou la fabrication de piscines.Ce type de résine sera à privilégier pour la fabrication de surfs, bien que certaines références de résines orthophtaliques présentent des propriétés comparables.
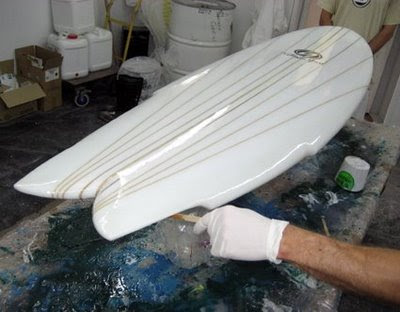
Résine isophtalique
D’une façon générale, ces résines présentent les qualités et inconvénients suivants :
QUALITÉS
Bon accrochage sur fibres de verre
Translucidité
Prix réduit
Mise en œuvre facile (basse pression)
Tenue en température (› 150°C)
Assez bonne tenue chimique
INCONVÉNIENTS
Inflammabilité
Émission de styrène
Durée de conservation en pot limitée
Retrait important (6 à 15 %)
Tenue vapeur et eau bouillante (pour orthophtalique)
Dans une résine commerciale, la résine est en solution dans un solvant, généralement le styrène. Le styrène contribue également aux propriétés finales des résines polyesters tout comme les polyacides et les polyols. En effet, il intervient à deux niveaux :
- Au cours du stockage où il sert à ajuster la viscosité de la résine. Il est alors considéré comme un solvant.
- Lors de la réticulation durant laquelle il joue le rôle d'un réactif à part entière. Ses groupements insaturés vont réagir avec les liaisons des polyesters pour former un réseau tridimensionnel infusible et insoluble.
Bien que l'utilisation d'autres monomères soit tout à fait envisageable, le styrène reste le monomère le plus performant pour diverses raisons ; Il est peu coûteux, sa fabrication est totalement maîtrisée et ses propriétés physiques sont idéales pour la mise en œuvre des résines polyesters insaturées. En revanche, il reste toxique et particulièrement visé par les réglementations.
Le styrène est un produit incolore dont la limite olfactive se situe environ à 0,3 ppm. Il est toxique pour les utilisateurs puisqu'il provoque des irritations et des troubles digestifs et du système nerveux central. Par conséquent, il est soumis à des réglementations strictes définies par le Ministère du Travail. La valeur limite moyenne d'exposition (VME) est fixée, actuellement, à 50 ppm (215 mg/m3) pour 8 heures d'exposition. La VME devrait diminuer dans les prochains mois.
.jpg)
Les émissions de styrène varient selon la technique de mise en œuvre et selon les étapes de la stratification. Elles sont maximales lors de la phase de mouillage de la fibre.
Les émissions de styrène dépendent notamment de :
- la teneur initiale de la résine en styrène (30 à 50 % en poids)
- la nature du catalyseur et des accélérateurs, entraînant un durcissement plus ou moins rapide
- la masse de résine mise en œuvre
- les conditions ambiantes de température et d’hygrométrie
Les résines polyesters insaturées classiques contiennent 45 à 50 % en poids de styrène, ce qui est relativement important. Le développement de nouveaux produits tels que les résines à faible taux de styrène (35 à 40 %) et à faible émission de styrène permettent de mieux répondre aux nouvelles réglementations.
D’autres monomères peuvent être généralement utilisés en tant que modificateurs du styrène en fonction de l'application visée. Par exemple, l'acétate de vinyle est ainsi utilisé pour la stratification des mousses sensibles au styrène (mousses PS et PVC). Les monomères acryliques permettent une diminution de l'indice de réfraction et une augmentation de la tenue à l'érosion et de la résistance aux chocs.
Les résines polyesters à faible émission et faible taux de styrène
-Les résines à faible teneur en styrène (FTS)
Comme leur nom l’indique, les résines FTS ont un taux de styrène nettement inférieur à celui des résines conventionnelles (35 - 40 % contre 50 %). Cette diminution de la quantité de solvant s’accompagne d’une augmentation de la viscosité devant rester compatible avec la mise en œuvre et la réticulation complète de la résine. Par conséquent, la formulation de base des polyesters est modifiée en incorporant des composés du type DCPD (Dicyclopentadiène).
Ce type de résine permet de diminuer fortement les émissions de styrène lors de l’imprégnation des renforts. Ce type de résines serait bien adapté à la fabrication des surfs, dans la mesure où le temps de gel de la résine utilisée est relativement court.
-Les résines à faible émission de styrène (FES ou LSE)
Ces résines contiennent un additif du type cire ou paraffine ayant une faible solubilité dans la résine. Ainsi, après application de la résine, l’agent filmogène forme un film protecteur en surface, empêchant l’émission de styrène durant la phase de durcissement. Néanmoins, elles peuvent présenter des problèmes de délaminage qui sont limités par l’incorporation d’agents d’accrochage. Ce type de résine permet de limiter essentiellement les émissions de styrène pendant la phase de polymérisation.
L’intérêt de ces résines est moindre pour la fabrication des surfs. Elles restent plus adaptées pour la
fabrication de pièces de grandes dimensions, nécessitant des temps de gels importants.
-Mélange de résine LES et FTS
La conjugaison de ces deux produits permet d’obtenir une réduction des émissions de styrène encore plus importante (émissions divisées par 3). En revanche, seulement quelques références commerciales sont disponibles pour l’ensemble des applications industrielles.
3. Les résines UV

Les résines réticulant sous UV semblent être, sur le principe, une solution technique intéressante pour limiter les émissions de styrène lors de la fabrication des surfs. Selon les cas, il serait possible de réduire de 60 g/m² l'émission de styrène.
Le durcissement des résines est initié par un rayonnement lumineux de longueur d'onde adaptée.
L’utilisation d’un catalyseur, de type péroxyde, n’est pas nécessaire pour assurer la polymérisation de la résine. Elles peuvent être mises en oeuvre par les procédés conventionnels. Elles sont ensuite soumises à un éclairage UV sous un champ de tubes luminescents (UV commerciaux, lampes de solarium). Comme la réticulation se fait dans le sens de la pénétration des UV, il se forme en quelques secondes en surface une peau durcie étanche au styrène. Les émissions ne sont donc pas diminuées lors de la stratification, mais lors du durcissement de la résine. Dès l'allumage des lampes, une couche durcie se forme en surface, suffisante pour empêcher l'évaporation du styrène.
Aujourd'hui, la plupart des résines polyesters standard ou vinylesters peuvent être formulées de manière à pouvoir réticuler lorsqu'elles sont exposées au rayonnement UV. Les formulations sont par exemple à base de cétones aromatiques comme initiateurs UV, utilisées avec des accélérateurs amines (méthyldiéthanolamine).

Afin d’assurer une bonne réticulation des résines UV, il est nécessaire de respecter quelques critères de mise en oeuvre.
Il est ainsi nécessaire de travailler avec des lampes dont la longueur d’onde est adaptée au produit.
Généralement, celles-ci fonctionnent dans une gamme de 360-420 nm. La puissance de la lampe et la distance de celle-ci à la pièce influencent la vitesse de réticulation. À noter, qu’il est possible d’utiliser des lampes qui n'émettent pas dans les courtes longueurs d'onde, ce qui permet d'éviter les problèmes potentiels pour la peau ou les yeux.

La lumière du soleil donne une réaction mais relativement lente. En revanche, une résine qui reste dans des locaux éclairés simplement par des ampoules à filaments reste utilisable.
Grâce à ce type de réticulation, les résines polyesters UV présentent de nombreux avantages par rapport aux résines classiques. Elles présentent un temps de gel infini tant qu'elles ne sont pas exposées aux UV de longueur d'onde adéquate, ce qui peut permettre de limiter la consommation de résine lors de la stratification. L’excès de résine d’une stratification peut être ainsi récupéré et utilisé pour le surf suivant.
D’autre part, l'utilisation de résines UV permet de réduire considérablement la quantité de solvants utilisés dans l'atelier en diminuant la fréquence de nettoyage des outillages, néfastes pour l'environnement et consommateurs de temps. Les outils peuvent donc n'être nettoyés qu'en fin de journée par exemple et leur durée de vie s'en trouve augmentée.

D’autre part, la polymérisation UV n'est possible que pour les systèmes transparents. Dans le cas de décoration des planches avec des « stickers » épais, il conviendra d’utiliser une résine catalysée normalement pour ces zones précises afin d’éviter les problèmes de résines non réticulées.
Le coût de ce type de résines est généralement largement supérieur aux résines standard (> à 3,5 Euros / kg).
4. Les résines époxy ou époxydes
Les résines époxydes (ou EP) résultent de la réaction de polyaddition de l’épichlorhydrine sur un polyol. La réticulation est basée sur la réaction des fonctions époxydes avec des durcisseurs, souvent de type amine permettant d’obtenir un réseau tridimensionnel.

Les kits commercialisés sont ainsi généralement constitués d’une partie A (la résine) et d’une partie B (le durcisseur).
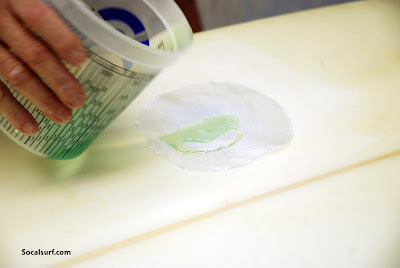
Les principales familles d’époxydes sont :
- Le diglycidyléther du bisphénol A (DGEBA), la résine la plus ancienne et la plus utilisée. À la base des systèmes dits "120°C", elle est souvent mélangée à des résines plus performantes pour améliorer la souplesse ou la mise en œuvre.

- Les diglycidyléther du bisphénol A et du tétrabromobisphénol A dont le comportement au feu est amélioré.
- Les Novolaques (EPN) présentant une meilleure tenue en température et une résistance chimique accrue.
- Les éthers de glycidyle de la méthylène dianiline (TGMDA), ils sont à la base des systèmes dits "180°C".
- Les époxydes cycloaliphatiques avec des propriétés mécaniques, électriques et de résistance au vieillissement supérieures.

Les durcisseurs les plus utilisés sont généralement des amines aliphatiques. Cette catégorie de durcisseurs permet des durcissements en 24 heures à température ambiante (la durée d’emploi est d’environ ½ heure à 1 heure). Un des plus célèbres est la triéthylènetétramine, ou TETA, qui confère des caractéristiques honorables mais a l’inconvénient de donner des allergies de contact.
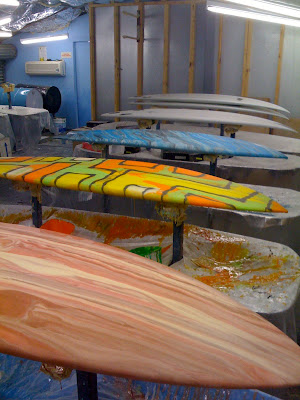
Les résines époxydes se différencient des résines polyesters par de bonnes propriétés mécaniques, une bonne tenue en température, un faible retrait et une faible absorption d’eau. En outre, elles peuvent présenter une grande résistance aux UV lorsque les formulations sont stabilisées. Ces résines sont généralement utilisées pour la fabrication de surfs rigides. Une post cuisson est toutefois souvent nécessaire pour stabiliser les propriétés de la résine.
En revanche, ces résines sont généralement beaucoup plus onéreuses que les résines polyesters.
5. Précautions d’hygiène et de santé.





Il convient déjà de prendre toutes les précautions habituelles pour la manipulation de n’importe quel produit chimique. C’est ainsi que les utilisateurs ne doivent poser en aucun cas des aliments sur une table servant à la manipulation des résines époxydes ou de leurs adjuvants et consommer de la nourriture sans s’être préalablement lavé les mains.

5.1. Problèmes cutanés.

En ce qui concerne le contact avec la peau, il faut savoir que le groupe époxydique est très agressif, du fait de la grande réactivité qu’il présente avec de nombreuses substances.
Les résines à base de bisphénol A non modifiées ne provoquent pas, en général, de dermatoses lorsqu’elles sont en contact avec la peau, car leurs molécules sont trop grosses pour pouvoir pénétrer facilement sous l’épiderme. Une résine à longue chaîne, par exemple semi-solide et, a fortiori une résine solide, présentent moins de risque qu’une résine liquide. Il faut surtout se méfier :
- des diluants réactifs dont la molécule est plus courte que celle des résines à base de bisphénol A (les résines diluées sont, de ce fait, plus à craindre que les résines non modifiées)
- de certains durcisseurs amines, comme le TETA (triéthylènetétramine) présentant une très basse viscosité, qui est susceptible de donner des allergies de contact. Et surtout les solvants qui abaissent la viscosité de la résine et qui véhiculent la molécule de résine sous la peau après avoir détruit d’ailleurs le sébum protecteur sécrété au niveau des pores de l’épiderme.

Les résines utilisées pour la fabrication de surfs sont généralement très fluides. Il convient donc d’être attentif aux risques d’allergie encourus.
Il faut donc proscrire tout solvant qui risquerait d’être employé pour le lavage des bras et des mains dans un atelier. Au contraire, il est vivement recommandé de se laver fréquemment les mains avec des savons spéciaux (par exemple des savons acides lorsqu’on manipule des durcisseurs basiques comme les amines aliphatiques), de garnir les établis de papier que l’on renouvelle chaque jour et que l’on jette après usage (et non de chiffons qui restent imprégnés de souillures et risquent de contaminer la peau).

Le port de lunettes et de gants de protection est obligatoire non seulement en des points critiques de l’atelier, mais aussi aux instants où certaines opérations dangereuses sont effectuées. Au besoin il est possible de s’adresser aux fournisseurs de résine afin d’obtenir les conseils de son spécialiste « hygiène et sécurité ». Si on ne respecte pas ces recommandations, il y a risque d’irritations des muqueuses oculaires et respiratoires et des zones sensibles (visage). Le risque est encore plus grand chez les personnes allergiques, en particulier en cas de manipulation de durcisseurs de type amine aliphatique.
D’autre part, il convient d’être particulièrement attentif à l’utilisation de certains durcisseurs amines qui peuvent être cancérigènes.
5.2. Problèmes oculaires
Si, à l’ouverture du couvercle d’un fût de résine ou de durcisseur, par exemple, un ouvrier reçoit du produit dans les yeux, il faut rincer la partie atteinte immédiatement et abondamment avec de l’eau, puis consulter un médecin en lui indiquant si possible la nature de ce produit. Normalement, le composant chimique principal est indiqué par le fabricant sur l’emballage.
5.3. Résines et cancers
Les résines polyesters utilisées avec la mousse polyuréthane contiennent du styrène qui est suspecté d’entraîner des cancers par inhalation pour les personnes qui l’utilisent. Le nombre de cancer prouvé par l’inhalation de styrène est relativement faible mais des risques existent.

Le styrène est également ingéré par les voies cutanées et par absorption au niveau des yeux, il convient donc de se protéger efficacement la peau et les yeux.
Un énorme merci à "Clean shaper" sans qui ce dossier aurait été encore plus fastidieux à monter !

